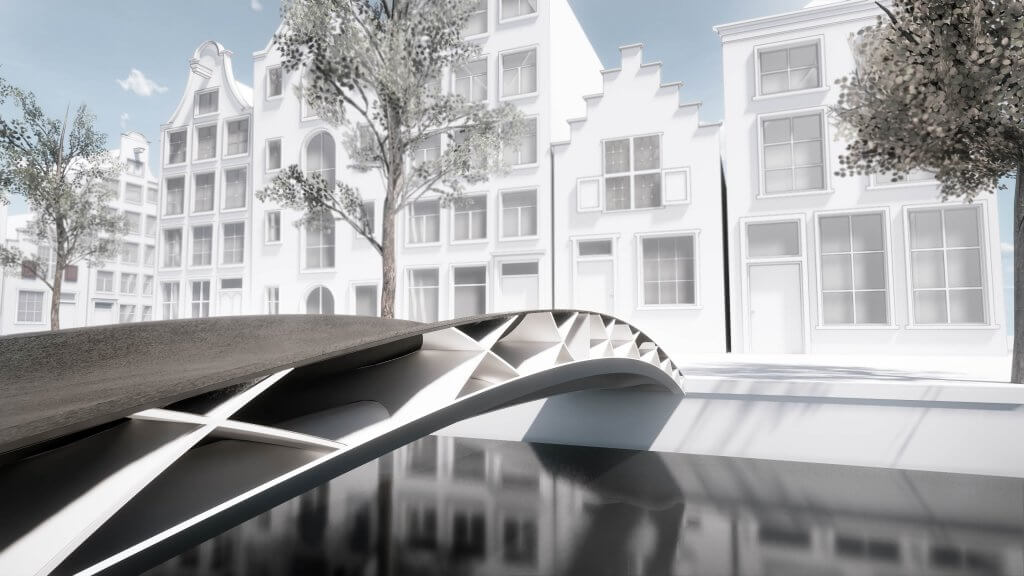
Trzy holenderskie firmy inżynierskie pracują nad budową mostu dla pieszych przy wykorzystaniu druku 3D.
Firma inżynierska Royal Haskoning współpracuje z firmą DSM i CEAD nad budową kładki dla pieszych. CEAD to firma z siedzibą w Delft (Holandia), która komercjalizuje proces ciągłego drukowania 3D wzmocnionego włóknami. Ich proces CFAM Prime może wytwarzać elementy wzmocnione włóknem szklanym lub włóknem węglowym o wymiarach do 4m x 2m x 1,5m. Materiały polimerowe wzmocnione włóknem węglowym mają szeroki wachlarz zastosowań, a swoboda tworzenia projektów pod druk 3D z zastosowaniem tych materiałów może prowadzić do zupełnie nowego sposobu konstruowania mostów i innych elementów konstrukcyjnych.
Urządzenia drukujące 3D z polimerów o dużych polach roboczych były dotychczas stosowane do np. tworzenia form odlewniczych, które wspomagają wytwarzanie dużych części do tuneli, mostów i innych części konstrukcyjnych. Systemy CEAD i BAAM eksperymentowały bezpośrednio z drukiem części konstrukcyjnych. Element drukowany w ten sposób , ma być pierwszą kładką dla pieszych wydrukowaną w 3D z polimerów.
Dzięki połączeniu polimerów z włóknem powstaje lekka i sztywna struktura o bardzo wysokiej wytrzymałości. Niektóre problemy niestety dalej pozostaną nierozwiązane, ponieważ struktura polimerowa wzmocniona włóknem może być zbyt krucha dla zastosowań mostów, duży wpływ mają także warunki atmosferyczne. Problemy tego rodzaju muszą zostać jeszcze rozwiązane przed wdrożeniem tych materiałów do tworzenia elementów konstrukcyjnych.
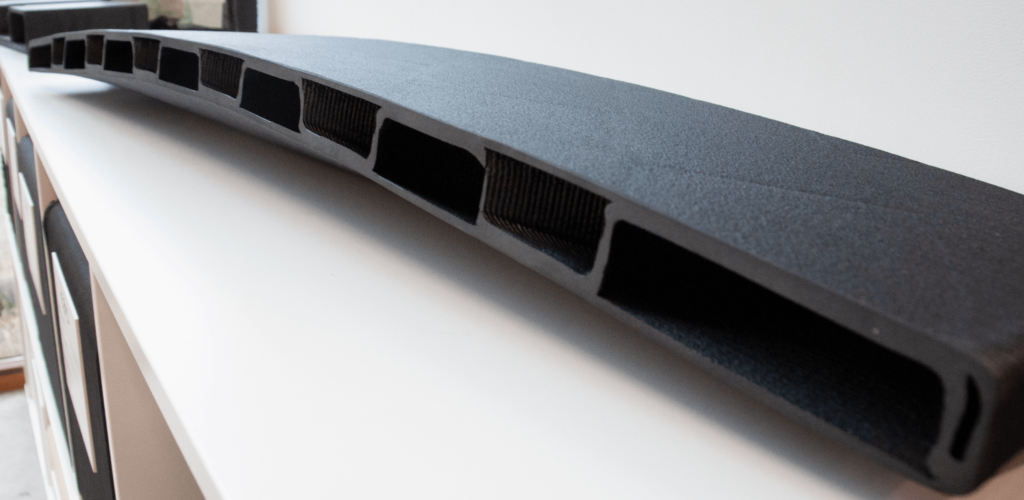
Mosty z tworzywa sztucznego wzmocnionego włóknem, znane są z długiej żywotności i niższych kosztów całkowitych w porównaniu z mostami stalowymi. Pierwszy w Europie most z tworzywa sztucznego powstał w Hesji w Niemczech w 2008 roku. Ma on aż 27 metrów długości, a jego płyty jezdne zostały wykonane z polimeru wzmocnionego włóknem szklanym.
Budowa mostu o betonowej konstrukcji trwa długo, co powoduje utrudnienia w ruchu drogowym, natomiast most ze wzmocnionego tworzywa sztucznego powstaje bezpośrednio w fabryce i zostaje w całości przetransportowany na docelowe miejsce. Montaż mostu na miejscu zajął… jeden dzień! To kolosalna różnica.
Ponadto koszty konserwacji to kolejny argument na korzyść tworzyw sztucznych. W przypadku tradycyjnych mostów często już po 15-20 latach konieczne są prace remontowe. Natomiast most z tworzywa sztucznego przewiduje się, że nie będzie wymagał napraw nawet przez 50 lat, gdyż materiał kompozytowy nie ulega korozji.
Ponadto aktualnie można użyć nowej technologii drukowania 3D, która powinna jeszcze bardziej obniżyć koszty całego przedsięwzięcia.
„Dodając czujniki do mostu, możemy z niego stworzyć „cyfrowego bliźniaka”. Czujniki te mogą przewidywać i optymalizować czas i datę konserwacji przez co zapewniać bezpieczeństwo i wydłużać czas eksploatacji mostów” – powiedział Patric Duis, segment lider w technologiach addytywnych
CEAD używa do drukowania metodę Fused Granulat Fabrication, która używa do druku granulat, zamiast wytworzonego z granulatu filamentu. Dzięki pominięciu jednej operacji w całym procesie drukowania, koszty końcowego wydruku maleją.
Patric Duis kierownik ds. innowacji w DSM powiedział:
Zamiast tradycyjnych materiałów, takich jak stal i beton, możemy tworzyć bardziej przyjazne dla środowiska mosty o bardziej elastycznym designie i co ważne, korzystając z materiałów nadających się do recyklingu. Skomplikowane projekty, które wcześniej były trudne, a nawet niemożliwe do stworzenia, można teraz wydrukować w 3D.
W związku z tak dużym problemem na świecie związanym z wytwarzaniem plastiku zespół będzie musiał wykazać, że te złożone materiały mogą zostać faktycznie przekształcone w coś użytecznego jeśli już nie będą potrzebne w formie pierwotnej. Wiele procesów recyklingu tych materiałów wymaga jeszcze opracowania, dlatego póki plan recyklingu nie jest jeszcze do końca przedstawiony – projekt jest jak na razie w strefie planów.
Cały projekt jest jak najbardziej ciekawy i widać w nim bardzo wiele zalet, jednak czuję pewnego rodzaju dysonans poznawczy czytają wypowiedź Pana Duis. Mówienie, że tworzenie z plastiku tak dużych konstrukcji jest „przyjazne dla środowiska” ponieważ jest możliwy do recyklingu jest sporym nadużyciem. Gdyby firma użyła plastiku z recyklingu (opcja wyłącznie hipotetyczna, ponieważ zdaje sobie sprawę z niskiej jakości takiego materiału) wtedy można by mówić o materiale przyjaznym środowisku, w innym przypadku materiały wykorzystany przez firmę jest po prostu lepszy od tych najbardziej popularnych materiałów (chociaż tak naprawdę bez wykształcenia budowlanego ciężko to ocenić.). Zamieszczam tutaj swój komentarz w tej kwestii ponieważ ostatnio nagminnie czytam o projektach, które określane są przez autorów jako przyjazne środowisku i ta fraza brzmi już jak populistyczne hasło mające na celu przekonać do swojego produktu, a nie jak fakt, który możemy wziąć za pewnik.
źródła: 3dprint.com i kopalniawiedzy.pl